Power modules versus discrete solutions - build or buy?
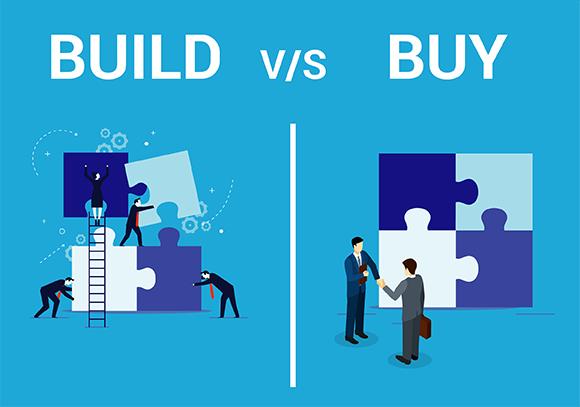
If you’re designing a power supply, it can feel like there are a million things to consider. You may be told you need to supply higher output power, or everything has to fit into a smaller space, and efficiency is important. More often than not, it also needs to cost less than the previous design, and the solution is needed in a challenging timeframe.
The requirements for power supplies are getting more difficult to meet, and time to market pressures can make the demands on engineers feel overwhelming. This can make off-the-shelf power modules an attractive option compared to the traditional route of building your discrete design. But can modules provide the right solution at a cost that competes with discrete alternatives?
Let’s start with the most apparent benefit of discrete solutions: the bill of material (BoM) cost is lower than with modules. However, using a module will substantially reduce the cost of design engineering, particularly for complex systems with multiple power rails. Beyond this, there are financial benefits from reducing time to market – in competitive industries, trimming a few weeks from development time can be crucial.
Another cost implication is the board space required. A module can put components on both sides of its PCB, potentially cutting the space required by 50%, and vertically-orientated packages can achieve even more space savings. Overall, these reductions in board space needed can make a big difference to total system cost.
In terms of layout flexibility, discrete designs can have the edge, and be customized to your specific requirements. Modules are limited to standard sizes, with pre-determined features and performance, so for some situations, the adaptability of discrete designs can be an advantage.
Of course, this assumes you have sufficient in-house power design expertise. Using modules makes implementation easier for non-experts, with support provided by the module vendor – both in terms of application engineers, and software tools to simplify the design process.
A discrete design will of course require many separate parts, including input and output capacitors, a power inductor, power transistors and a controller. All of these components must be carefully chosen, with performance depending on getting the correct values. Once a system design is completed and produced, using a modular solution can make it easier to find a second source, as modules typically follow industry-standard footprints.
Having more parts can be complicated for purchasing departments to handle too, with a higher risk of sourcing components and reliability issues. Sourcing a module on the other hand can be much simpler, and with the flexibility offered by digital solutions in particular, a single part number can be used for a multitude of different output voltages.
When it comes to quality and reliability, a module will provide a proven, qualified design with known characteristics and factory burn-in to screen out infant mortality, so reliability is likely to be much higher. In the event that there are problems, replacing a module is easy, and the module vendor will be responsible for finding the root cause and implementing any corrective actions.
The module will also complete appropriate safety tests during qualification and production, reducing the testing required by the power system designer. In fact, it can be complicated with a discrete design to isolate the power system from the rest of the circuit, and test it appropriately. Tracing faults can be challenging and time-consuming, and in the worst case, an entire board may need to be scrapped.
Looking at performance, in a discrete design, power and signals will typically use the same host PCB, which makes it more difficult to optimize thermal design. Instead, a module will often use a thick copper multi-layer PCB, improving thermal performance and reducing parasitic issues.
Overall, discrete components may initially seem appealing due to a lower perceived BoM cost. However, power modules can often be the most economical option long-term – and provide multiple advantages in terms of being more accessible and offering faster design cycles, with lower risk.
If you want more advice or want to work with Flex Power Modules solutions on your next design, then get in touch today.