Scaling new heights with vertical power delivery
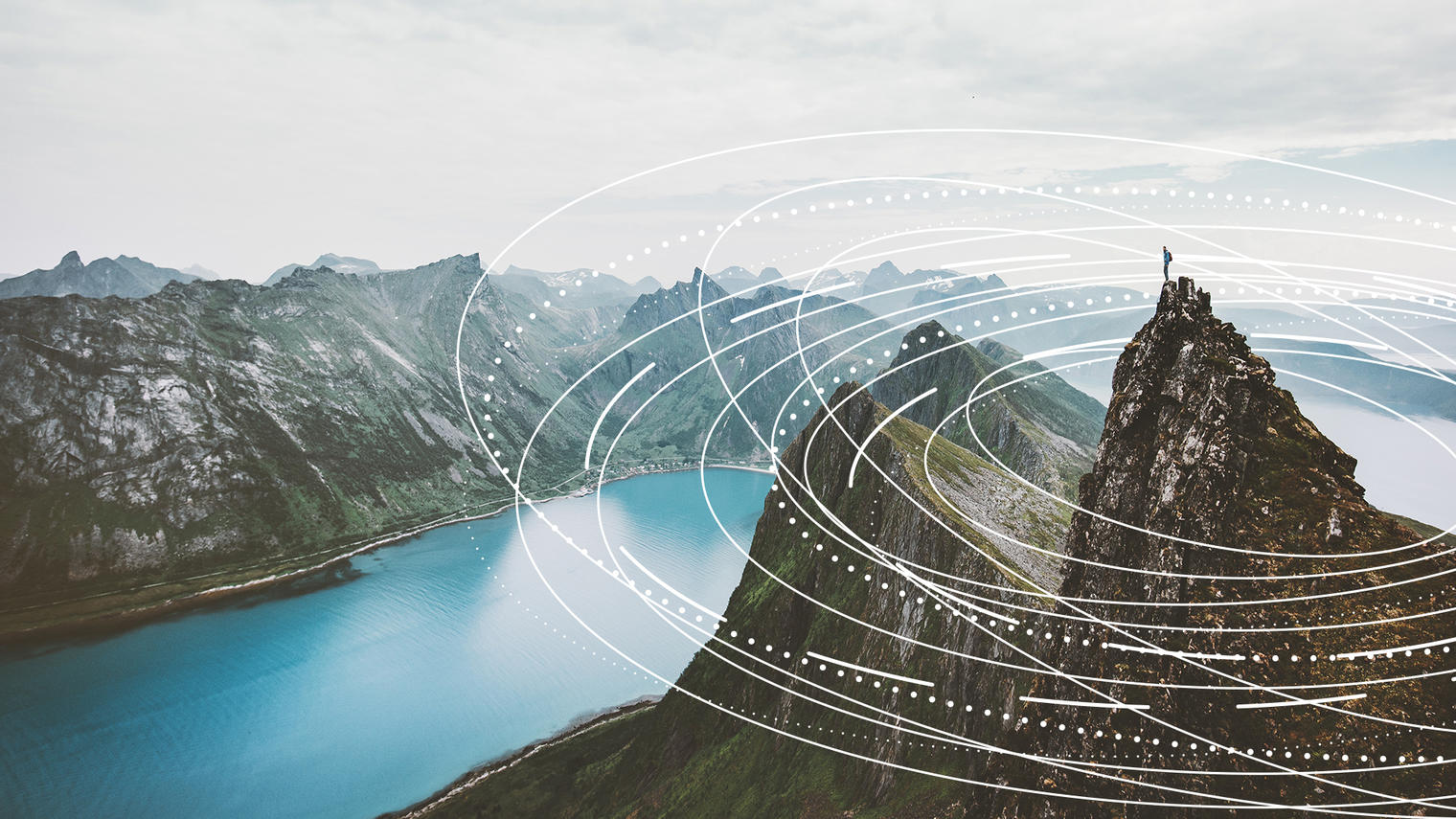
The effects of AI and ‘big data’ are all around us, from the humble home assistant with an almost uncanny ability to emulate human thinking and come back with instant information, to the control of vast factories through edge computing and the cloud. The incredible performance comes down to fast self-learning software algorithms and chips in servers that now have transistor counts in the billions. These CPUs, GPUs, FPGAs and ASICs can’t be physically any bigger though with the increase in data processing demand – they must be compact to maintain speed, and data center managers need to pack ever-more server blades in a rack to achieve best utilization of space and hardware.
Current draw goes up with data throughput
Laws of physics must prevail and power consumption by these ICs has also increased significantly, even if the performance per watt has increased, such that hundreds of amps are drawn continuously with peaks of over a thousand along with high current slew rates. Designers have reduced power rail voltages to minimize the resulting extra dissipation, but this complicates the power distribution network (PDN) design. As a result, common schemes are to do power conversion in steps with ‘intermediate bus converters’ (IBCs) followed by ‘point of load’ converters (PoLs) or Voltage Regulator Modules (VRMs) to minimize losses (Figure 1). The PoL/VRM is placed as close to the end load as possible on the same lateral plane, but at the highest currents the connection distance when located alongside the load still produces voltage drops along tracks, both from resistance and inherent inductance, compromising performance.
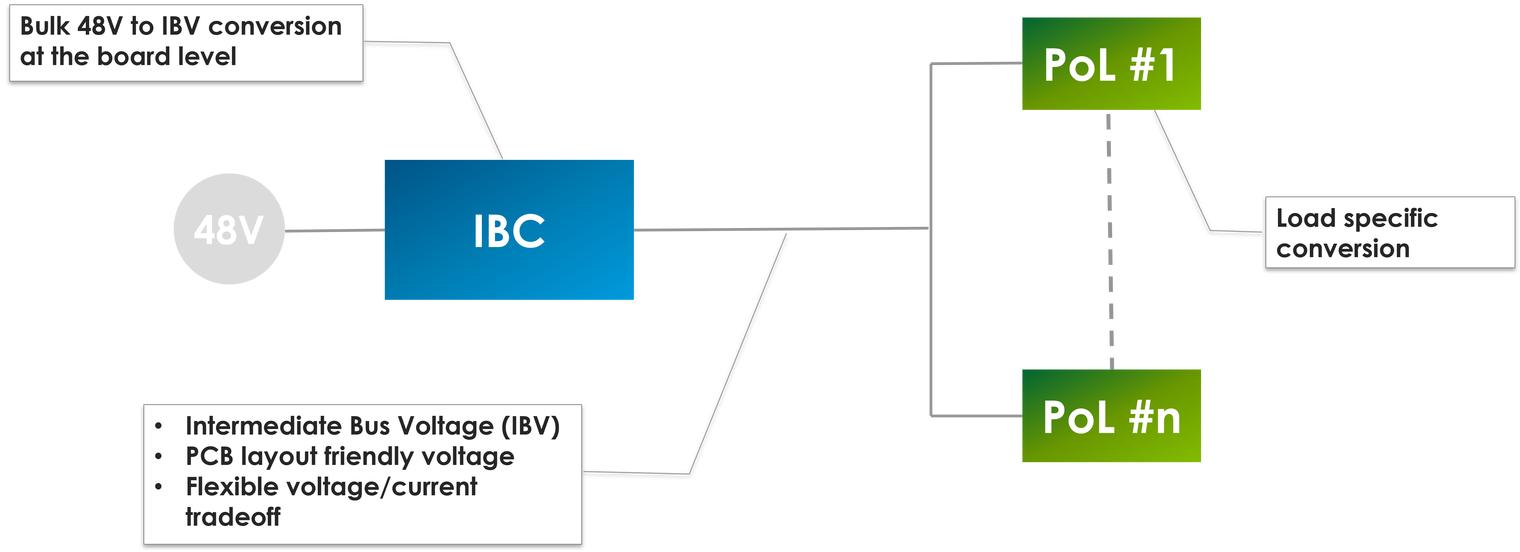
A solution is to instead put the PoL/VRM directly underneath the chip for the closest possible connection, and this is an approach enabled by the latest customized products and design capabilities from Flex Power Modules. Termed ‘Vertical Power Delivery’ modules, the DC/DC converters have pinouts customized to directly match the processor pinout with up to 2400 solder balls, and are low profile to enable bottom-side mounting. The placement of the conversion stage directly under the load minimizes the distance that the high currents need to travel, hence significantly reducing the PDN resistances and losses, helping both system efficiency and load transient response.
An example proposal of a VPD module which can implement 8-32 phase power conversion with 1-7 voltage rails is shown in Figure 2.

This recent example of a custom device developed for a key customer is rated to 670 A continuous/1300 A peak and operates over an input range of 5-7.5 V with an output programmable from 0.6-0.9 V and an efficiency rating of 86%. An external controller assembly is needed, which was also developed by Flex Power Modules, which can handle sixteen parallel phases and includes monitoring and alarm functions. Physically, this example is 22 x 43 x 6 mm and includes 800 solder balls for its BGA connections. Heat generated is removed by a cold plate, typically liquid cooled, on the ‘top side’ of the module where the power semiconductors are mounted with co-planar surfaces.
VPD solutions are best customized
For an optimal solution, the VPD module is designed as a custom for the application with the pin-out matching the target load chip, and electrical specification tailored to suit. This will define the number of power phases and voltages while the thermal performance of the VPD is matched to the cooling available, usually so called “Direct to Chip” or D2C cooling. Flex Power Modules then works with the customer to meet the power and cost budgets, time frame and performance requirements requested.
The future of VPD devices
Flex Power Modules offers custom design development to expand the scale of their VPD range, keeping pace with the requirements of the industry for ever-higher peaks in current demand while maintaining power quality. Look out for the next pinnacle to be scaled and Flex Power Modules flag to be planted.