Sustainability in research & development
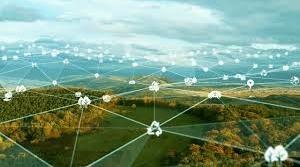
Introduction
The World Economic Forum (WEF) has identified the electronics industry as one of 8 sectors which together account for more than 50% of global carbon emissions[1]. Meanwhile, researchers at the University of California have found that GHG emissions from electronic devices and their associated e-scrap increased by 53% between 2014 and 2020, with 580 metric tons emitted in 2020, or around 4% of total global GHG emissions. With the current growth rate of the industry, the UCI researchers estimate that emissions from the industry, if unchecked by regulation, will reach around 852 million tons by 2030.
As global efforts to reduce emissions increase, leading industry players such as Flex are responding by both participating in and complying with evolving carbon accounting regulations and practices.
In this second blog post in a series describing how Flex Power Modules is improving the sustainability of its operations, we focus on the research and development process.
R&D and the sustainability challenge
The US EPA estimates that between 70% and 80% of the environmental impact of a product is determined during the R&D phase of the product life-cycle, highlighting the importance of a sustainable approach to R&D. At the same time, the WEF reports that 77% of the electronics industry’s emissions are Scope 3 emissions, meaning they are attributable to the supply chain, including both upstream and downstream activities.
It is therefore not sufficient for industry leaders such as Flex to control Scope 1 and Scope 2 emissions, we have a responsibility for the sustainability of our entire supply chain. Our R&D function, at the front-end of the development process, plays a key role in controlling Scope 1, 2 and 3 GHG emissions by designing for sustainability across the life-cycle of a product.
R&D at Flex Power Modules
At Flex Power Modules we have been progressively transforming our R&D function to ensure that sustainability joins features, performance, and cost as a core design objective at the outset of any new project. The remit of the Flex Power Modules R&D function is not just to design products with sustainability of manufacturing in mind, but also to improve sustainability throughout the product life-cycle. This involves reviewing sourcing policies and supply chain partners, as well as our own sales and distribution operations. The way in which our customers use our products must also be accounted for, so that designs can focus on efficiency during operation, extension of life-cycles, and reduction of waste at end-of-life.
For over 20 years, Flex Power Modules has rigorously applied Design for Environment (DfE) techniques, principles, and methodologies in all product development projects. DfE requires companies such as Flex Power Modules to apply Life Cycle Thinking, (LCT), when designing a new product, to maintain or improve quality and cost while reducing environmental impacts. LCT covers five aspects of the product life-cycle, figure 1, including raw material extraction, manufacturing, packaging and distribution, use and end-of-life.

Figure 1: Life Cycle Thinking covers five aspects of the product lifecycle
This approach has led to a radical overhaul of Flex Power Modules reliability testing process. The use of regenerative loads has significantly lowered electricity consumption and, at the same time, by introducing recirculated cooling, waste water has been totally eliminated from its previous level of 500,000 m3 per annum. Refrigeration chambers used in the process have also been upgraded to newer, more efficient models which use environmentally friendly liquids.
The Flex Power Modules’ DfE approach has also resulted in the introduction of restrictions on our use of hazardous substances including lead mercury, cadmium, and hexavalent chrome, ensuring our compliance with RoHS and REACH directives. Our products and processes also comply with Flex Power Modules’ own lists of banned substances which include those covered by the RoHS and REACH directives as well as an extensive list of other substances which are either banned, restricted or under observation due to environmental regulations or concerns.
DfE also drives the design and development of high-efficiency DC/DC power modules that decrease the energy consumption of our end-customers’ applications, reducing their Scope 1 GHG emissions and our Scope 3 emissions. The innovative adoption of digital control technology on Flex Power Modules pioneering BMR453 series of quarter brick isolated DC/DC converters, for example, reduce our customers emissions in several ways. The modules achieve efficiency levels of up 96.1%, reducing the carbon footprint of our customers’ products. As well as improving energy efficiencies, this approach contributes to lower total cost of ownership for our customers by impacting the dimensioning and cost of system components. The higher levels of integration achievable with the digital controller IC result in fewer components such as cooling fans, air-conditioning units, heatsinks, power supplies, and battery back-up capacity. The smaller bill-of-materials improves sustainability through reduced electrical waste at end-of life and also reduced test and verification and handling procedures as well as a reduction in required documentation.
Sustainability begins with R&D
Measuring and controlling Scope 3 emissions are widely recognized as key to any organization’s overall sustainability plan and carbon accounting standards are increasingly focused on measuring and controlling them. R&D can significantly influence Scope 3 emissions, by evaluating sourcing options based on sustainability criteria and also by designing energy efficient products with minimal waste at end-of-life. At Flex Power Modules, our R&D function is at the heart of our sustainability approach, and we will continue to monitor and adopt leading practice approaches, in line with the Flex ESG plan.
[1] Net-Zero Challenge: The supply chain opportunity,” World Economic Forum, Jan. 2021
Previous blogs available in this series:
Part 1: Sustainability in Production