Paralleling DC/DC power modules: what you need to know
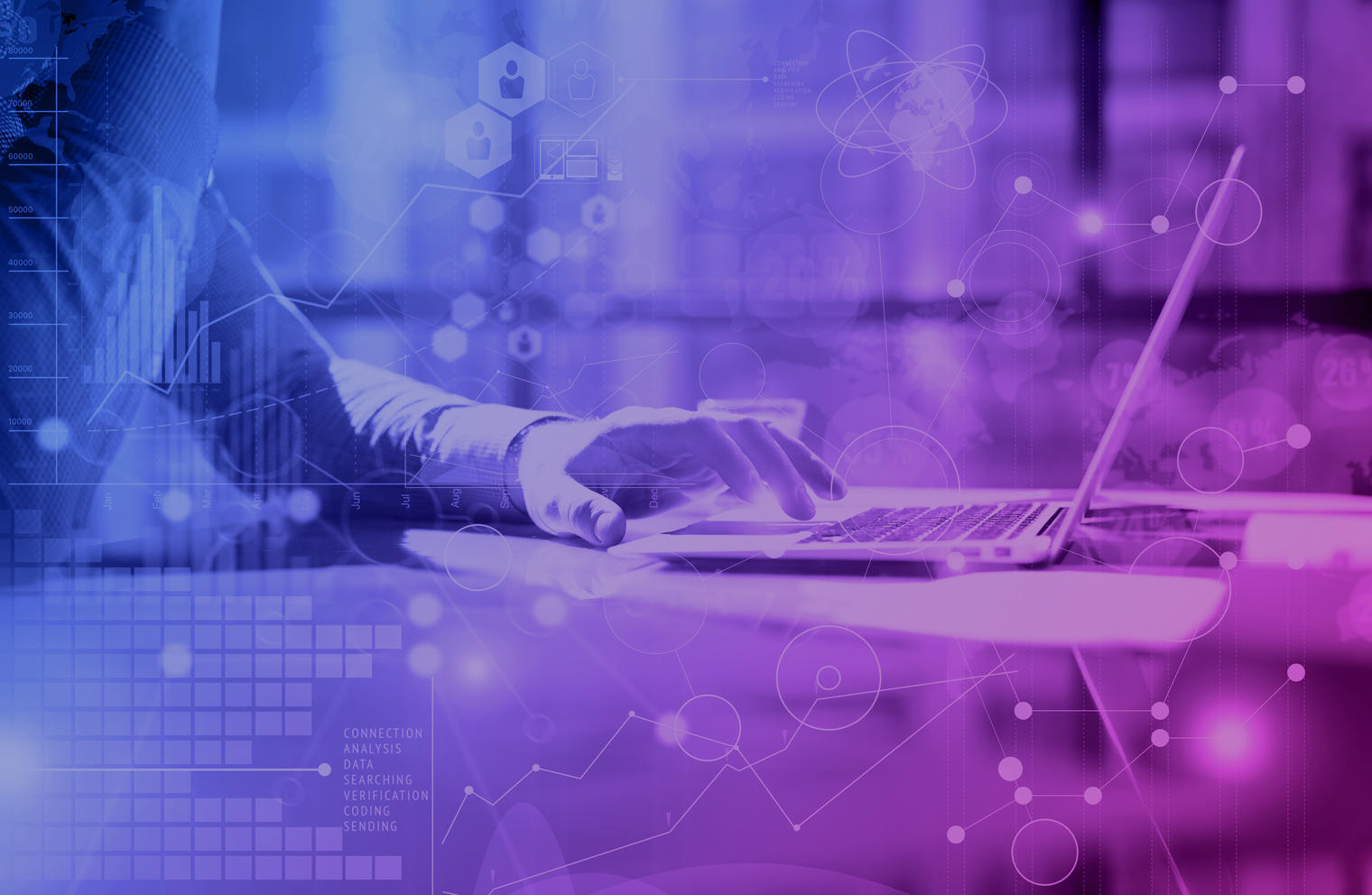
Reasons for Paralleling
Firstly, you may need more current than a single power module provides. Using two modules in parallel, the current to the load can be effectively doubled. Paralleling can also reduce the number of different power module types used, by meeting higher power requirements with lower power modules in parallel.
Why not just use a big power module instead of paralleling? Bigger modules might be less efficient than their smaller counterparts, and bigger passives will be required, which take up space. Designing such power systems is not straightforward, either – sometimes paralleling is the easier and quicker option. Also, using two smaller DC/DC power modules will spread the heat dissipated across a larger PCB area, helping reliability.
A second reason is providing redundancy in high-reliability systems. With more converters available than required to provide the total load current, if one fails, the same amount of current can still be delivered. Popular schemes are N+1 (with one redundant converter), N+M or even 2N for high levels of redundancy.
Load Sharing
Two DC/DC converters connected in parallel may not automatically share the load equally. Even if they’re identical, the output voltages will differ slightly due to component tolerances. The one with the higher output voltage will typically provide the entire load current, operating at its limit while its partner is doing little work – thus creating a thermal hot spot, and reducing its expected lifetime.
Additionally, when paralleling for redundancy, if modules are loaded unequally and the one providing most of the current fails, its partner must quickly increase its load from minimal to the maximum. This causes undesirable transients and a temporary drop in output.
There are two main methods to parallel converters and ensure a converter is not overloaded:
- Droop Load Sharing (DLS) – the converter is designed with a “soft” output voltage vs. current characteristic. This causes the output voltage of each converter to automatically adjust downward as current increases, so that each converter approximately shares the total output current.
- Active Current Sharing (ACS) – a more complex design, normally used on higher power converters. A signal line connects the paralleled converters and actively controls their internal switching operation as a function of the sensed current level in each converter.
The advantage of DLS is simplicity - modules are just connected in parallel. The disadvantage is the droop voltage from no load to full load. Load sharing accuracy is based on the unit to unit output voltage setpoint range and the droop slope.
Another option exists when using converters without current-sharing provisions but with the capability of external voltage adjustment. There are ‘load sharing’ integrated circuits available that can be connected externally to adjust the converter output voltages to achieve the desired sharing of current.
Paralleling Capabilities
Not all modern DC/DC converters can be paralleled, or they may be limited to paralleling for redundancy rather than current sharing. Check the manufacturer’s datasheets or contact your Flex representative for advice.
Many power modules from Flex are designed for easy paralleling, such as PKM4817LNH, which achieves current sharing without the need for any external components or connections. Flex Power Modules' latest Design Note describes the parallel operation and load sharing of its products in greater detail, and discusses design considerations to optimize current sharing for maximum output power.
For more about paralleling, read our Design Note DN006 ‘Using analog isolated DC/DC power modules in parallel configurations’.
To keep up to date with our latest Product News and Announcements, please sign-up to our Newsletter