What's driving the need for halogen-free products?
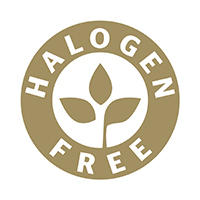
About halogens
There has been increasing concern about ‘halogens’ in electronics - the five or sometimes six, chemically-related group 17 elements in the periodic table. Actually, the focus is on bromine and chlorine – of the other halogens, fluorine is not currently a concern, iodine is not generally used and astatine never is, being a rare radioactive element. The sixth, tennessine, has only been made in the lab and again decays very quickly with largely unknown properties and is not used.
Elemental chlorine and bromine are highly toxic and certainly do not appear in the make-up of electronics, but organobromides are used as flame retardants in PCBs, molding compounds, adhesives, solder masks, cable insulation and flexible circuits, while polyvinyl chloride or PVC is very common as insulation and as a mechanical damping material. The most common use for bromine and chlorine compounds is as a flame retardant, and of course, this is a good thing, to mitigate the effects of burning components causing dangerous fires. It can also be said that in normal use and eventual professional recycling of electronics, bromine and chlorine compounds do not pose a significant hazard - they are only seen as problematic in the illegal and unregulated burning of the electronics, sometimes carried out to recover valuable metals such as copper. At high temperatures, bromine and chlorine compounds can release dioxins which are Persistent Organic Pollutants (POPS) known to be carcinogenic, and furans which are toxic and possibly carcinogenic. The levels of these chemicals released is however mixed with intake from many other sources. For example, the US Environment Protection Agency estimate that more than 90% of dioxins are actually ingested from animal fats [1]. Also, furans appear and are accepted in staples such as roasted coffee and processed baby foods at a low level [2].
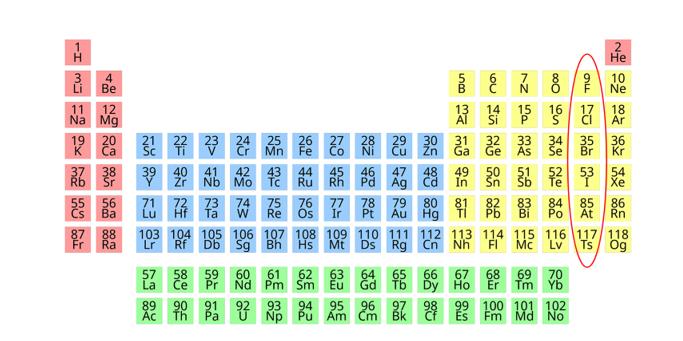
Picture 1: The halogens in the periodic table
Halogen-free is not mandatory
Unlike with the RoHS and REACH directives in Europe and their equivalents round the world, which have banned certain substances by law, there is no statutory requirement to eliminate halogens from electronic equipment. There are however standards which make recommendations, for example, for circuit boards, IEC 61249-2-21 sets compliance limits of 900ppm by weight of PCB material for bromine, 900ppm for chlorine and 1500ppm for the total of the two. If the limits are not exceeded, a supplier can claim ‘halogen-free’ status. Another standard, JS709C, covers electronics more generally and has slightly higher limits for materials other than circuit boards of 1000ppm by weight for bromine from brominated flame retardants (BFRs), and 1,000 ppm of chlorine by weight from chlorinated flame retardants (CFRs), polyvinyl chloride (PVC) congeners and/or PVC block polymers, copolymers or polymer alloys containing PVC. Under these limits, the material can be identified as ‘low halogen’ according to JS709C. Under some circumstances higher levels are permitted in plastics as long as they are not flame retardants, PVC or containing PVC.
Halogen-free may attract a premium but can have performance advantages too
In response to health concerns and with standards setting voluntary limits, some manufacturers of products are anticipating regulation and asking their suppliers for ‘halogen-free’ components including PCBs, plastics and other non-metallic materials. To achieve this and still maintain flammability ratings, alternative materials must be used and for circuit boards for example, phosphorous or nitrogen can be used in the resin as flame retardants. Halogen-free or ‘green’ molding compounds, adhesives, and other materials are also available but require very careful qualification for the electronics applications to ensure that product reliability is maintained under all environmental conditions. Characteristics that must be evaluated include at the minimum: coefficient of thermal expansion (CTE), glass temperature (Tg), moisture absorption, adhesion strength and flexural modulus.
Although in some cases halogen free materials can be more expensive, for example solder paste and circuit boards, other replacement materials such as adhesive can actually be lower cost, but in total there is expected to be a small premium to pay for halogen-free. There are advantages other than environmental however, halogen-free circuit boards can have better dielectric breakdown ratings, lower coefficient of thermal expansion, higher glass melting point, Tg, which enables higher operating temperature and lower moisture absorption rate.
Flex Power Modules is responding
Flex Power Modules has researched the topic of converting products to halogen-free and with appropriate material changes, DC/DC conversion products BMR491 and BMR492 have been shown to achieve compliance to the IEC 61249-2-21 limits. Reliability tests and analysis of field data are ongoing and further products in the range are queued for conversion. Products that are destined for customers that are involved in more commercial type end-uses are prioritized before those for telecom applications, where the application environment is assumed to be relatively inaccessible to persons and eventual disposal of equipment as waste will be tightly controlled. For very cost-sensitive, high-volume applications, customers may still have the opportunity to request a non-halogen-free product. Requests for conversion of a particular product to halogen-free earlier than programed can be considered depending on circumstances, and new products in certain application areas will be developed halogen-free from the outset.
Conversion to halogen-free is a journey, and inevitably more chemicals might be identified for exclusion in the future - antimony for example. Flex Power Modules will stay at the forefront of materials technology to ensure that their customers’ products remain as safe as possible for the environment and its inhabitants.
[1] https://www.epa.gov/dioxin/learn-about-dioxin
[2] Moro, S.; Chipman, J. K.; Wegener, J. W.; Hamberger, C.; Dekant, W.; Mally, A. (2012). "Furan in heat-treated foods: Formation, exposure, toxicity, and aspects of risk assessment" (PDF). Molecular Nutrition & Food Research. 56 (8): 1197–1211.