Connecting Flex Power Modules’ solutions in parallel or series
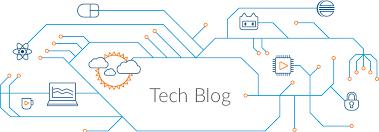
We know that sometimes an application comes along where one power module is simply not enough to provide the required voltage or current. So, what are the options?
Connecting two or more converters in parallel can provide the solution as it increases the available load current and, therefore, the load power. However, caution is required. For instance, many assume that parallel configuration is fine providing you use two DC/DC converters of the same specification – the thinking being that this strategy will ensure equal load sharing. And yet, even connecting two identical power modules in parallel will result in unequal load sharing due to component tolerances. The module with slightly higher output will end up supplying the entire load current, with the other offering precious little. Operating life may well reduce due to the creation of a thermal hot spot.
To circumvent this situation, you can adopt a DC/DC converter that takes advantage of droop load sharing (DLS) or active current sharing (ACS). Although the former benefits from a simple design, the latter is advantageous for higher power systems. Equal load sharing through DLS or ACS minimises the dynamic response required from each converter, resulting in less disruption to the output.
We hear a common question: why not simply use a bigger power module instead of using two smaller ones in parallel? In short, bigger converters might be less efficient than their smaller counterparts, and will require bigger passives, which demand space. What’s more, you’ll find that deploying two smaller DC/DC power modules can spread the dissipated heat over a larger PCB area, aiding reliability.
Astute product choice
In terms of product selection, the potential for parallel connection is device-dependent, so you should always consult the technical specification and/or check with the supplier. It’s important to remember that not all modern DC/DC converters have the capability for parallel connection, at least not without external current-share control circuitry. Others may be limited to paralleling for redundancy rather than current sharing.
The inherent design of our PKM4817LNH DC/DC converter, for example, makes it very easy to connect in parallel. Using DLS, the converter effectively offers a ‘soft’ output voltage versus current characteristic. As a result, the output voltage of each converter adjusts downwards automatically as current increases, ensuring that each converter shares the total output current. The upshot is that this power module achieves current sharing without the need for any external components or connections.
Other power modules, such as our PKB-C, PKB-D, PKJ, PKM-A, PKM-D, PKM-NH (except the aforementioned PKM4817LNH), PKU-C, PKU-D and PKU-S series, require an external current-sharing integrated circuit wherever there is a need for parallel configuration. Due to active rectification (for high efficiency), an ORing circuit (diode or MOSFET) must be used on each module’s output - even in parallel - for increased power. Without this component, the module’s rectifier will suffer damage due to reverse current. Reference designs for such circuits are available on our Design Note 006.
In terms of layout, our best-practice advice is to connect the outputs together as close to the load as possible. Furthermore, avoid connecting diodes or other current-blocking devices between the inputs of paralleled products. Maintaining low resistance and inductance between the inputs is another good strategy.
Products that provide ACS include the BMR4910202/853 and BMR4800112/032 digital intermediate bus converters, for example. In this case, a signal line connects the paralleled converters and actively controls their internal switching operation as a function of the sensed current level in each converter, achieving extremely high sharing accuracy.
Connecting devices in series
For those applications that need higher voltages rather than higher currents, it’s also possible to connect power supplies in series. To provide an example, designers can connect the outputs of two 30 V converters in series to produce a 60 V rail. The load voltage will be the sum of the output voltages of all power supplies in series. However, the load current will be restricted to the power supply with lowest load current capability. As a further caveat, it may be necessary to include protection circuitry to disable one device if the other turns off for any reason. This technique can be very useful if you have an unusual voltage requirement, or cannot find a single standard module solution to a particular need.
For further information on using our converters in your application, please contact our team of expert applications engineers, who will be happy to support your designs with their know-how and experience: pm.support@flex.com