High profile gets you noticed and frees up board space
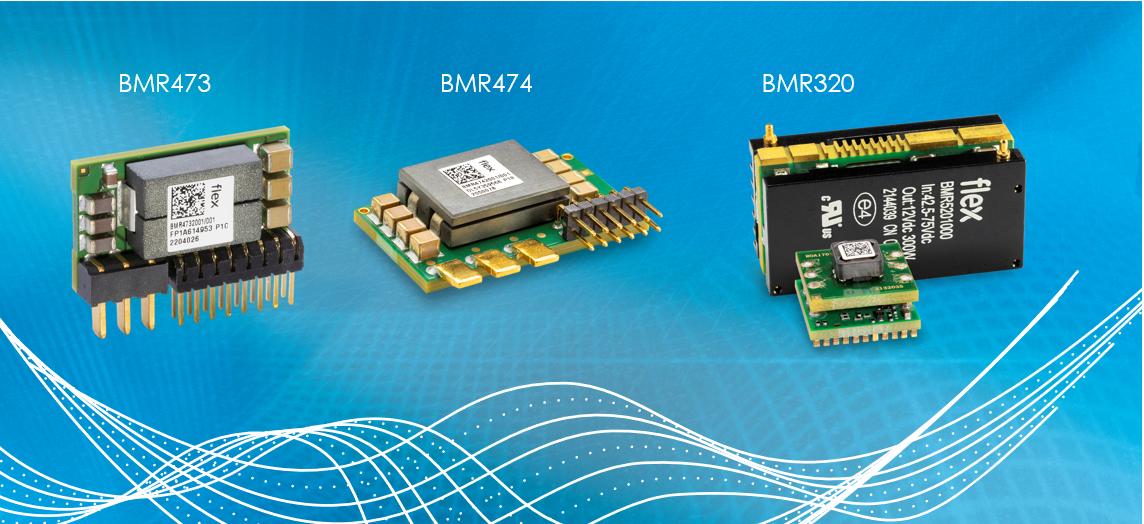
In many electronics applications, low profile components are used so that more cards can be designed into a rack. However, keeping a low profile doesn’t always suit the high packaging density of modern electronics, particularly in server racks where the “XY” space is limited but “Z” height is available. In these types of applications, keeping to a maximum height and minimizing the XY dimensions can pack more functionality into a card and get the eventual benefit of more functionality per square meter of Data Center floorspace.
DC/DC Power modules that are in a vertical format with minimal footprint therefore can have their place - look inside any desktop PC and you will see them as VRMs supplying the Point-of-Load power for CPUs with their tall heatsink and fan assemblies. Complex arrangements of heat pipes and bracketry can apply heatsinking to a vertical module, but as general-purpose products, they have to be characterized to operate with convection or forced air cooling with an integral heatsink. The problem is now knowing what air is available, how hot it is already from adjacent heat-dissipating components and what flow rate is practically achieved. Modern power modules are achieving astonishing efficiency figures with dissipation of only a few watts when loaded at hundreds of watts, but that load may be only a few centimeters away, upstream in the airflow and raising the local ambient temperature to a high level.
Thinking in the third dimension
At high power, even the lowest profile DC/DC converters typically need attached heatsinks, raising the overall height and adding the expense and cost of sourcing and attaching it, effectively suspended above the other board components. There may be other components that set the height necessary, such as connectors, on-board fans or large capacitors. In other circumstances, the constraint may be PCB XY footprint area occupied, where a conventional ‘brick’ module, perhaps with a ‘keep-out’ area underneath, is using too much valuable board area that is needed for other components or tracking.
Vertical power modules can be a valuable solution
When a ‘holistic’ approach is taken however, the vertical approach can add value. Latest vertical IBC products can pack 900 W rating into a footprint slightly less than the size of a horizontal quarter brick of the same power. In addition, a vertical IBC can have an integrated wraparound heatsink which effectively doubles the cooling surface area, allowing for efficient cooling even with moderate airflow. The heatsink can also be engineered to be optimum for the module, with the lowest thermal resistances to components, compared with low-profile baseplate cooled types that have to thermally interface with an external heatsink or cold plate, leading to variability in insulation and flatness, especially when multiple modules are fixed.
One potential problem with high-power vertical modules could be the mechanical mounting - for example due to a high center of gravity and significant weight, SMD terminations alone may not be robust enough to secure the module through shock and vibration testing. Through-hole terminations have generally been preferred for the mechanical support they provide, perhaps with additional mechanical screw fixings, however that makes for a somewhat more inconvenient and expensive assembly.
A Vertical DC/DC power module can deliver 300 W in less than 7 cm2 footprint
An example of the effective use of vertical power modules is seen with the Flex Power Modules BMR520 product (Figure 1). This is termed a ‘power blade’ and is a full-function 300 W isolated DC/DC converter with 42.5-75 V input and 12 V output. With its SMD mounted footprint of 17 mm x 40 mm and maximum heatsinking area in a height of 20 mm, the blade forms a power conversion stage, driven by a separate control assembly in conventional horizontal PCB SMD format.
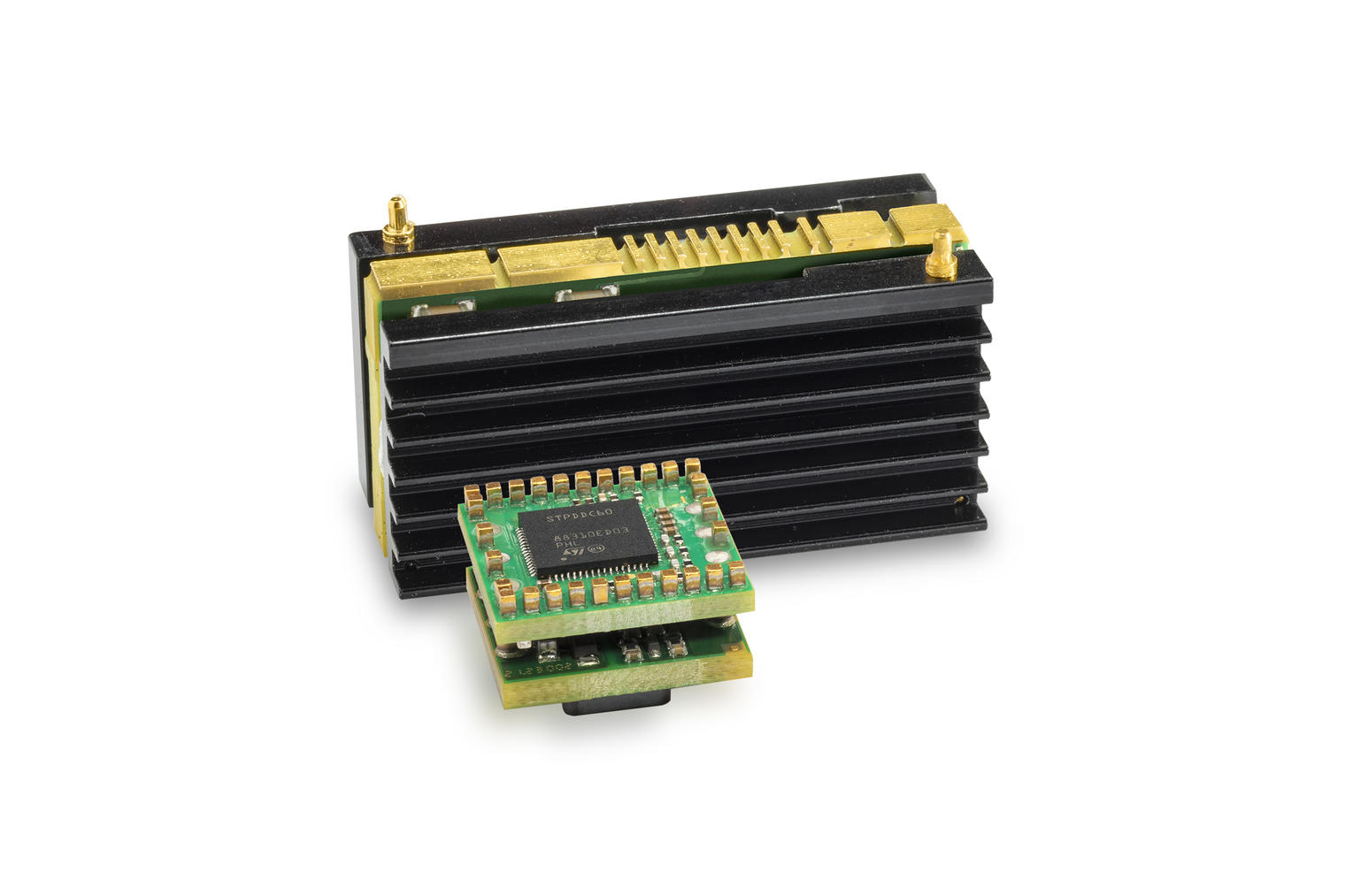
Figure 1: Flex Power Modules BMR520 (300 W) vertical DC/DC converter with control assembly
The control assembly includes all control, monitoring and protection features and is PMBus® enabled. The blade’s integrated heatsink covers the two long sides of the module for maximum surface area and effective dissipation of heat, and this, along with a high conversion efficiency of around 94%, allows operation to over 80°C air temperature with sufficient air flow, at 48 V input. The small control assembly, just 17 mm x 17 mm, is fitted adjacent and can drive up to three blades for 900 W total output. Splitting the control and power stages gives flexibility for 1, 2, or 3 Blades based on power draw, but also reduces the weight of the power stage so that it can be safely surface-mounted with normal automated assembly including two mechanical support through-hole pin-in-paste connections. There is opportunity now to orient the vertical module to make the best use of available airflow and even to be inventive and use the part as a ‘baffle to redirect hot air away from sensitive downstream components. Small footprint blades can also be easier to fit into a typical board layout than one larger quarter-brick (typically 58.4 x 36.8 x 12.19 mm)
Non-isolated power modules have their place too
The BMR520 would typically be followed by non-isolated point-of-load converters and in environments where there is height available, ‘SIP’ style PoL modules can again occupy small footprints for significant power output. For example, the through-hole BMR474 series from Flex Power Modules can supply up to 80 A / 198 W in a board area of just 33 mm x 12.1 mm with an integrated heatsink and 3 m/s airflow. A version with a footprint of just 33 mm x 8.6 mm will also provide 80 A with the same airflow but derates from a lower temperature in natural convection. Product height in each case is just 19 mm. Also available shortly in the SIP format is the BMR473 delivering up to 40A housed in a package measuring just 26.3 (L) x 8.8 (W) x 15.6 (H) mm.
Going for a high profile can be a good thing, especially when you are trying to maximize use of the board space available. It needn’t be at the expense of thermal or electrical performance though – both the BMR520 and BMR474 are supported by the Flex Power Designer software so you can model the significant benefits available.